|
|
|
In
our integrated-manufacturing cycle the blank goes
through various processes while being transformed
from the raw material to the end product. Each
stage in the manufacturing cycle has in-built
quality checks which ensure that the end product
will conform to all relevant quality parameters.
|
|
Turning Department
Here the forged blanks are turned to suit
the drawing requirement on CNC machines.
Necessary supporting equipments for drilling,
tapping, broaching, key-way slotting etc. are also
installed.
|
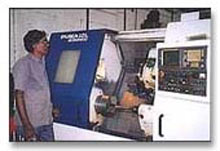 |
|
Gear
Cutting Department |
|
The Gleason® Five Cut method is followed for
Spiral Bevel Gears and Crown Wheel and Pinions
manufacturing. Our products conform to AGMA
standards. Gears are cut by using the Generation or Format®
method and Pinions are made using the Three Cut
Gleason Cycle.
Before the cutting commences, the cutter blades
are mounted on the cutter head and trued radially
and axially.
The re-sharpening of the blades are done on
special purpose cutter grinding machines.
|
|
Straight
Bevel Gears are cut on machines using the Coniflex®
System. This system of cutting ensures
high productivity and good surface finish.
Cutter blades are re-sharpened radially and
axially on special purpose cutter sharpening
devices.
|
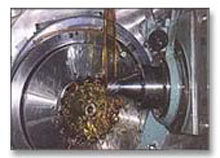 |
|
Spline
Hobbing & Thread Milling:
Splines are hobbed on imported Spline hobbing
machines and threads are milled on imported
special purpose thread milling equipment.
|
|
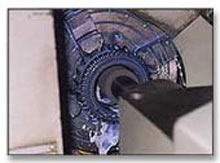
|
Grinding Department
In our recent expansion program we
have installed the latest machinery for internal,
cylindrical
spline
and surface grinding.
The internal diameter of hardened crown
wheels are ground by holding the component
in pitch
line chucks to ensure accuracy of the
finished gear.
|
Heat Treatment
Department
Each component is gas carborised in an pit
type furnace, then hardened in oil electrical degreased and then tempered. The component
is then shot blasted.
To ensure low distortion while hardening, Crown
Wheels are
press quenched i.e. the component, while hot, is
held in a custom made die and immersed in
quenching oil. Care is taken to ensure that the
part is always pressed under controlled pressure while
being quenched.
Some components are cooled to
sub-zero
temperatures, using special application
low-temperature
equipment,
to get
better micro structure. Some components are sharpened to get better life and stress control.
|
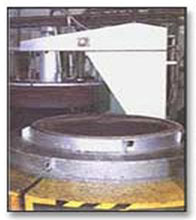 |
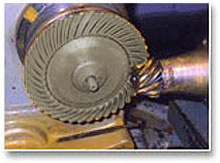
|
Lapping Department
To ensure smooth and quiet running,
the Gears
and Pinions are lapped after hardening.
Lapping is accomplished by running mating
pairs together in a Gleason® Hypoid lapping
machine and feeding a liquid abrasive
compound under pressure into the gear pair. The
compound removes small amounts of metal as the
gears rotate, thus refining the
tooth surface and achive desired contact pattern.
|
 |
|
|
|
|
|